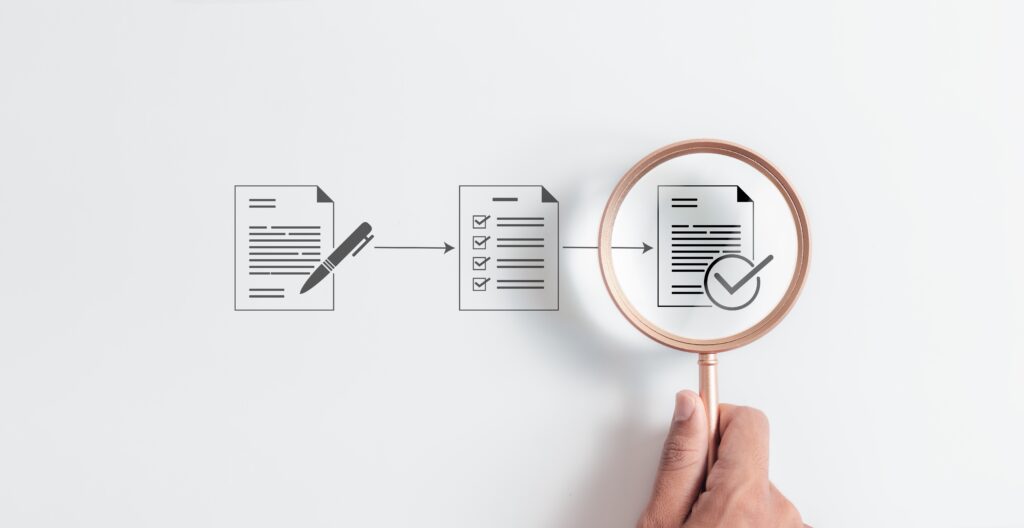
EU GMP explained
The European Union (EU) Good Manufacturing Practice (GMP) guidelines for pharmaceutical manufacturing establish strict standards to ensure the quality and safety of medicinal products. These guidelines outline different “Grades” for cleanrooms, which are classified based on the level of cleanliness and environmental control required during various stages of drug production. The four primary GMP Grades in the EU are Grade A, B, C, and D.
Grade A
Usage:
- This is the highest level of cleanliness and is used for critical zones where sterile products are exposed to the environment (e.g., filling and closing operations).
Environmental Conditions:
- Air Particles: Must maintain less than 3,520 particles (0.5 microns) per cubic meter during operation.
- Microbial Contamination: Should have less than 1 colony-forming unit (CFU) per cubic meter.
- Airflow: Typically requires unidirectional (laminar) airflow with a velocity of 0.36–0.54 meters per second.
Grade B
Usage:
- Serves as a background environment for Grade A zones, usually in the same room where the critical process is carried out.
Environmental Conditions:
- Air Particles: Must maintain less than 3,520 particles (0.5 microns) per cubic meter during operation.
- Microbial Contamination: Should have less than 10 CFUs per cubic meter.
Grade C
Usage:
- Used for less critical stages of production, such as the preparation and handling of components and solutions to be subsequently sterilized.
Environmental Conditions:
- Air Particles: Must maintain less than 352,000 particles (0.5 microns) per cubic meter during operation.
- Microbial Contamination: Should have less than 100 CFUs per cubic meter.
Grade D
Usage:
- Applied to less critical areas for handling of components after the initial preparation and handling but before final sterilization.
Environmental Conditions:
- Air Particles: Must maintain less than 3,520,000 particles (0.5 microns) per cubic meter during operation.
- Microbial Contamination: Should have less than 200 CFUs per cubic meter.
Key Concepts and Requirements
- Air Quality: The primary factor distinguishing the grades is the air cleanliness, specifically the concentration of airborne particles and viable microbial contamination.
- Environmental Monitoring: Continuous monitoring of particulate and microbial contamination is crucial, particularly in Grades A and B.
- Airflow Patterns: Grade A environments require laminar airflow to minimize contamination risks. Grades B, C, and D have progressively less stringent airflow requirements.
- Pressure Differentials: Controlled pressure differentials between areas of different grades help prevent contamination flow from less clean to cleaner areas.
- Cleaning and Disinfection: Each grade requires specific cleaning and disinfection protocols to maintain the required level of cleanliness.
- Personnel Requirements: Higher grades require more stringent gowning and hygiene practices to minimize human-related contamination.
Implementation
- Design and Construction: Cleanrooms must be designed to prevent contamination through careful control of materials, surfaces, and environmental parameters.
- Validation and Qualification: Regular validation of cleanroom conditions and qualification of equipment and processes ensure compliance with GMP standards.
- Documentation and Records: Meticulous record-keeping of environmental conditions, cleaning procedures, and personnel training ensures traceability and accountability.
Understanding these GMP Grades helps pharmaceutical manufacturers maintain high standards of product quality and patient safety by ensuring a controlled and contamination-free production environment.
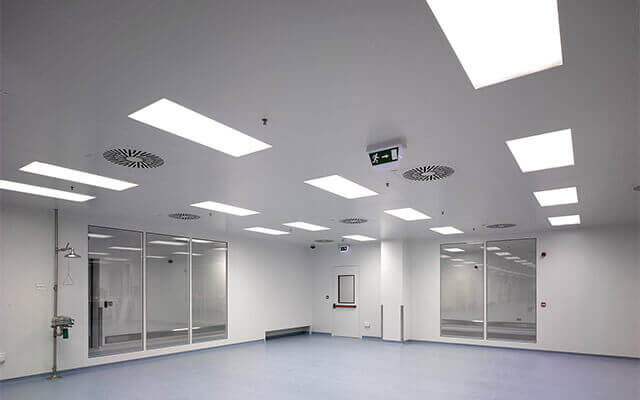
Want to know more ?
To find out more about any of our products or services please contact us for further information.
News
July 9, 2024
What is a cleanroom and how is it graded?
In today’s world, where precision and cleanliness are paramount, the concept of a cleanroom has become indispensable across various industries….
Read More